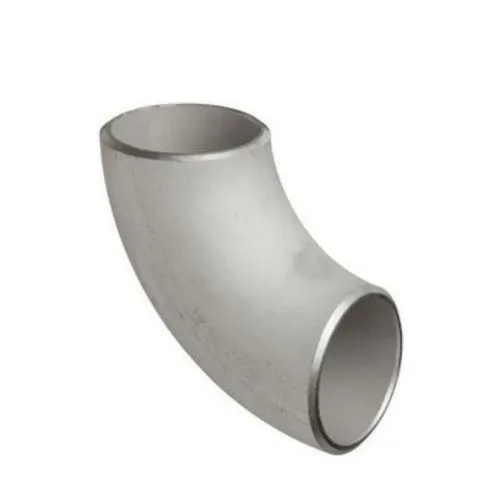
What is a butt weld elbow? A butt weld elbow is a type of pipe fitting used to change the
Sino Special Metal supply below ranges for the stainless steel pipe and tube:
Standards: ASTM A312, ASTM A213, ASTM A269, ASME SB677
Duplex stainless steel pipe standards: ASTM A789/ ASME SA 789. ASTM A790/ ASME SA 790
Material: AISI 304, 304L, 316, 316L
Outer Diameter: 5.8-508mm
Wall Thickness: 0.3-50mm
Share:
A stainless steel pipe is a type of cylindrical conduit or tube made primarily from stainless steel, a corrosion-resistant alloy. Stainless steel is composed of iron, chromium, nickel, and other elements, depending on the specific grade. The inclusion of chromium in the alloy provides the primary characteristic of stainless steel, which is its resistance to corrosion and staining.
Stainless steel pipes are used in a wide array of applications, including plumbing, industrial pipelines, automotive exhaust systems, heat exchangers, structural components, and more. The choice of grade and type of stainless steel pipe depends on the specific requirements of the application, such as the level of corrosion resistance needed, temperature conditions, and mechanical properties required.
Stainless steel pipes can be categorized into two primary manufacturing processes: seamless and welded. Additionally, stainless steel pipes can come in various shapes and forms based on the manufacturing process and requirements. Here’s an overview of these categories:
1. Seamless Stainless Steel Pipes:
– Manufacturing Process: Seamless stainless steel pipes are made from solid round billets of stainless steel. They are heated and pierced to form a hollow tube, followed by additional processes to size and finish the pipe.
– Advantages:
– Superior strength and integrity due to the absence of a welded seam.
– Suitable for high-pressure and high-temperature applications.
– Smooth internal surface, reducing friction and promoting fluid flow.
– Applications: Chemical processing, oil and gas exploration, high-pressure applications, and where corrosion resistance is critical.
2. Welded Stainless Steel Pipes:
– Manufacturing Process: Welded stainless steel pipes are made by joining two separate pieces of stainless steel through various welding methods. Common welding methods include TIG (Tungsten Inert Gas), MIG (Metal Inert Gas), and laser welding.
– Advantages:
– Cost-effective production.
– Availability in a wide range of sizes and shapes.
– Suitable for less demanding applications.
– Applications: Structural applications, plumbing, automotive exhaust systems, and general-purpose piping.
3. Special-Shaped Stainless Steel Pipes:
– Manufacturing Process: Special-shaped stainless steel pipes are created by shaping the stainless steel into non-standard forms. These can include hexagonal, equilateral triangle, octagonal, and other custom shapes.
– Advantages: Used for specific applications where standard cylindrical pipes are not suitable.
– Applications: Architectural design, artistic projects, and specialized industrial applications.
4. Hot-Rolled Stainless Steel Pipes:
– Manufacturing Process: Hot-rolled stainless steel pipes are formed by rolling steel at high temperatures.
– Advantages: High strength and surface finish.
– Applications: Structural components, machinery, and large-diameter pipes.
5. Cold-Circular Stainless Steel Pipes:
– Manufacturing Process: Cold-circular stainless steel pipes are created by cold-drawing a seamless pipe through a die.
– Advantages: Precise dimensions and improved surface finish.
– Applications: Precision tubing for various industries, including automotive and instrumentation.
Each type of stainless steel pipe has its own advantages and is chosen based on factors such as the application, required performance, cost considerations, and specific dimensional requirements. The choice between seamless and welded pipes, as well as the selection of special shapes or standard cylindrical forms, depends on the needs of the project or industry.
By offering super austenitic stainless steel pipes and tubes in different material standards and grades, SSM provides customers with the flexibility to choose the specific material that best suits their unique application requirements. This enables industries to benefit from the exceptional properties of super austenitic stainless steel in challenging and aggressive environments, where corrosion resistance and durability are of utmost importance.
Certainly, here are explanations for the common standards related to stainless steel pipes and tubes that you mentioned:
1.ASTM A312:Standard Specification for Seamless, Welded, and Heavily Cold Worked Austenitic Stainless Steel Pipes
ASTM A312 is a widely used standard that covers seamless, welded, and heavily cold-worked austenitic stainless steel pipes. It specifies the dimensions, mechanical properties, and testing requirements for these pipes. This standard is often used for general-purpose stainless steel pipes in various industries.
2.ASTM A213:Standard Specification for Seamless Ferritic and Austenitic Alloy-Steel Boiler, Superheater, and Heat-Exchanger Tubes
ASTM A213 covers seamless ferritic and austenitic alloy-steel tubes for use in boilers, superheaters, and heat exchangers. It provides requirements for the chemical composition, mechanical properties, and testing of these tubes. This standard is crucial for applications involving high-temperature and high-pressure conditions.
3. ASTM A269:Standard Specification for Seamless and Welded Austenitic Stainless Steel Tubing for General Service
ASTM A269 specifies the requirements for seamless and welded austenitic stainless steel tubing for general service applications. It outlines the dimensions, mechanical properties, and various testing methods for these tubes. ASTM A269 is commonly used for tubing in industries like pharmaceuticals, food processing, and instrumentation.
4.ASTM A789/ASME SA789: Standard Specification for Seamless and Welded Ferritic/Austenitic Stainless Steel Tubing for General Service
ASTM A789 and ASME SA789 are specifications that cover seamless and welded ferritic/austenitic stainless steel tubing for general service applications. The materials covered by these standards are often referred to as duplex stainless steels. They offer a combination of high strength and corrosion resistance, making them suitable for various industries.
5. ASTM A790/ASME SA790: Standard Specification for Seamless and Welded Ferritic/Austenitic
ASTM A790 and ASME SA790 are specifications that cover seamless and welded ferritic/austenitic stainless steel pipes. Like A789/SA789, these standards apply to duplex stainless steel pipes, which are used in demanding environments where corrosion resistance and strength are critical.
6.ASME SB677:Specification for UNS N08904, UNS N08925, and UNS N08926 Seamless Pipe and
ASME SB677 specifies the requirements for seamless pipes and tubes made from specific high-corrosion-resistant materials, including UNS N08904 (904L), UNS N08925, and UNS N08926. These materials are used in industries like chemical processing and offshore oil and gas due to their excellent corrosion resistance properties.
These standards play a crucial role in ensuring the quality, compatibility, and performance of stainless steel pipes and tubes in various applications and industries by providing specific guidelines for material composition, manufacturing processes, and testing procedures.
The manufacturing of stainless steel pipes involves various processes depending on the type of pipe being produced. Here’s an overview of the common manufacturing types and processes for stainless steel pipes:
1. Seamless Hot Rolling Processes:
– Round Pipe Billet: The process begins with a round billet of stainless steel.
– Heating: The billet is heated to the required temperature for easy forming.
– Perforation: A hole is pierced through the center of the heated billet.
– Three Roll Skew Rolling, Continuous Rolling, or Extrusion: The billet is subjected to one of these processes to reduce its diameter and elongate it into a pipe shape.
– Off Pipe: The formed pipe is cut to the desired length.
– Sizing (Or Reducing Diameter): The pipe may undergo further sizing or diameter reduction processes to meet specific dimensional requirements.
– Cooling: The pipe is cooled to stabilize its structure.
– Straightening: To ensure the pipe’s straightness.
– Water Pressure Test (Or Flaw Detection): The pipe may undergo testing to check for any flaws or imperfections.
– Marking: Pipes are marked with relevant information such as size, material, and standards compliance.
– Storage: The finished pipes are stored for distribution or further processing.
2. Seamless Cold Rolling (Cold Drawn) Processes:
– Round Pipe Billet: Same as in the hot rolling process.
– Heating: The billet is heated.
– Perforation: A hole is pierced through the billet.
– Head: The pipe is shaped and sized using a head.
– Annealing: The pipe may undergo annealing to relieve stresses and improve its structure.
– Pickling: The pipe is pickled to remove any oxide or scale.
– Oil (Copper): Surface treatment may include oiling or copper coating.
– Multi-Pass Drawing (Cold Rolling): The pipe is drawn through dies to reduce its diameter and achieve the desired shape.
– Heat Treatment: Heat treatment may be applied to further adjust the properties of the pipe.
– Straightening: To ensure the pipe’s straightness.
– Water Pressure Test: The pipe undergoes a water pressure test.
– Marking: Pipes are marked for identification.
– Storage: Finished pipes are stored for distribution or further processing.
3. Longitudinal Welding (Straight Seam Welding) Processes:
– This category includes processes such as Electric Resistance Welding (ERW) and Electric Fusion Welding (EFW).
– Instead of starting with a single billet, it involves forming a pipe by longitudinally welding a flat strip or plate.
– ERW uses electric resistance to create a weld, while EFW uses an electric arc to fuse the edges of the strip or plate.
– These processes are often used for producing welded stainless steel pipes, which can be more cost-effective than seamless pipes for certain applications.
These manufacturing processes are essential for producing stainless steel pipes with different characteristics, such as seamless or welded, and meeting specific dimensional and quality requirements. The choice of process depends on the intended use and the desired properties of the final product.
Our stainless steel pipes and tubes are renowned for their exceptional corrosion resistance, strength, and durability. Whether you require seamless or welded solutions, we have you covered. Our products adhere to stringent international standards, ensuring that you receive reliable and top-notch materials for your applications.
Stainless steel pipes and tubes find applications in a wide array of industries, including but not limited to construction, automotive, chemical processing, and food production. With Sino Special Metal, you can expect superior products that deliver outstanding performance in various environments.
Explore our comprehensive selection of stainless steel pipes and tubes, and feel free to reach out to our expert team for guidance or to place your order. We are committed to providing you with the finest stainless steel solutions to meet your specific requirements. Choose quality, choose Sino Special Metal.”
What is a butt weld elbow? A butt weld elbow is a type of pipe fitting used to change the
At SINO SPECIAL METAL, we provide high-quality butt weld eccentric reducers, essential fittings used in piping systems to seamlessly connect
What is a Butt Weld Concentric Reducer At SINO SPECIAL METAL, we offer high-quality butt weld concentric reducers, pivotal components
SSM stands as a premier supplier enterprise, renowned for its specialization in crafting high-quality special metal products. Our commitment to excellence and precision in production ensures that your unique metal requirements are not just met but exceeded. Discover the quality that defines SSM as a leading name in the industry.